SAW Devices
Background
Surface acoustic wave (SAW) devices have been known for several decades. Although their main use has been mainly in Telecommunications as resonators and filters, they can also be used as sensors (possibly with wireless interrogation capabilities) and identification tags (RFIDs).
Most SAWs depend on the propagation of mechanical waves in the surface of a solid. Although there are several types of surface waves, in this context the relevant ones are Rayleigh waves, in which the trajectories of the solid particles is elliptical (figure). They propagate at speeds that are of the order of 10–5 of the speed of light, depending on the materials, and they only penetrate the solid up to a depth comparable with the wavelength. At 1GHz, for most materials, this is typically a few micrometers.
For their use as electrical components, a SAW device depends on the successful conversion of electrical signals into mechanical vibrations. This is achieved by coupling a piezoelectric substrate with an electrode structure that allows the conversion of electrical signals into mechanical waves propagating through the substrate. Such a structure is called an interdigitated transducer (IDT) of which a simple implementation is shown on the figure.
Note that only the material directly underneath the IDT needs to be piezoelectric. Also, such a structure is reversible, being capable of both electromechanical and mechanoelectric transduction.
SAW-based Sensors
Sensors use the change in propagation characteristics of the material due to a number of physical factors. A simple structure is shown on the figure.
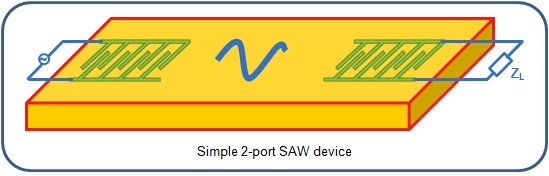
One of the IDT’s converts electrical energy into mechanical energy, thus operating as a transmitter, the other one operates as a receiver. Due to the low speed of the surface waves, the transit delay is relatively large and can easily be measured using electronic techniques. Any physical magnitude that causes a change in this delay can thus be converted in an electric signal. SAW’s have successfully been used as sensors for, among others
- mass
- strain/stress
- force
- torque
- humidity
- chemical concentration.
If the signal source is an antenna, the SAW becomes a wireless device, in the sense that it can be remotely interrogated. The output can be fed to another antenna or, if the receiving IDT is configured as a reflector, the device will respond with a delay that is a function of the physical parameters of the medium.
SAW-based RFIDs
A receiving IDT can easily be made to operate as a reflector. The electrical load can be reflected as a mechanical load, and as in any transmission line, depending on the value of the load some of the energy can be reflected and some absorbed. By arranging a series of reflectors along the path of the mechanical wave, a signal can be detected at either end of the transducer that, given an appropriate code, can be associated to different transducers.
Thus an SAW can be made to operate both as an RFID and a sensor for a wide range of physical magnitudes. The use of wireless interrogation is very attractive due to two main factors:
- The device can be used for sensing physical magnitudes in inaccessible, harsh or hostile environments, as no electrical connection between the sensed medium and the readout device is needed;
- There is no need for a local power supply, as the device gets power from the interrogating RF beam.
Note that the first of these advantages is valid only insofar as the device itself can survive the hostile environment. Most of the piezoelectric materials found in today’s SAW’s have some limitations in this respect.
SAW Devices and Diamond
The increasing demand for higher frequencies requires higher SAW velocities. Very high values of frequency may be reached by combining at the same time the high phase velocity of diamond and a significant reduction of the IDT period.
Diamond is a very interesting material from several points of view. It is a semiconductor with very low electrical conductivity, but with a very high thermal conductivity. Its fusion temperature is also one of the highest of all materials known to man. It is also one of the hardest materials known, and along with this has a very high compliance. This, along with the fact that nowadays there is a wide choice of techniques for depositing diamond, or diamond-like carbon, on various substrates, would make diamond an almost ideal medium for the implementation of SAW devices, if it weren’t for the fact that diamond, exhibiting a symmetrical crystalline structure, is not piezoelectric. Several instances of depositing diamond on piezoelectric substances, thus profiting from the advantages of both materials, have been tried.